U of T researchers develop foam filter system to mop up oil spills faster

Associate Professor Amy Bilton, left, and fellow team members Calvin Rieder, Puwaner Gou, Nitish Sarker, along with Jordan Bouchard (not pictured), show off a prototype of their polymer foam filter technology (photo courtesy of Monisha Naik)
Published: August 1, 2024
A research team from the University of Toronto has advanced to the final stage of a national competition that seeks to develop better ways to protect Canada from the devastating effects of oil spills.
The team, led by Amy Bilton, an associate professor of mechanical and industrial engineering in the Faculty of Applied Science & Engineering, has been awarded $1.3 million via Natural Resources Canada’s (NRCan) Oil Spill Response Challenge to develop and test a system that treats contaminated water onboard oil spill response ships.
Called FRODO, the prototype allows for treatment of contaminated water stored in response vessels through an engineered polymer foam filter – not unlike a kitchen sponge – that allows water to pass while syphoning off the small oil particles. The filter and treatment system would allow the ship to release previously contaminated water back into the environment. That, in turn, means more oil can be collected in less time.
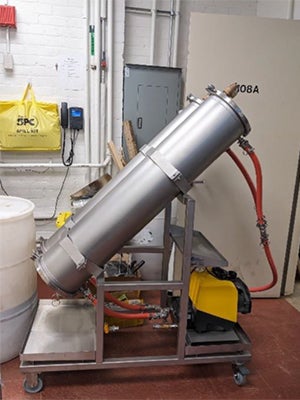
By contrast, current approaches involve response vessels gathering oil with large, floating barriers before using a skimmer to suck oil and water into their holds. The ships must then offload the entire load – about 25 per cent oil and 75 per cent water with small trace amounts of oil – to a land-based facility for treatment.
“We’re both engineering the foam material and developing the treatment process to fill in a gap in current oil spill operations,” says Bilton. “We aim to increase the amount of oil these vessels can collect by a factor of four.”
More than four million barrels of oil are transported through Canada daily. With more than 240,000 kilometres of coastline and more than 890,000 kilometres of freshwater systems across the country, effective oil spill response is critical in protecting diverse ecosystems and communities. Through the Oil Spill Response Challenge, the Government of Canada is investing $10 million in the development of innovative and rapidly deployable solutions to oil spill detection, response and recovery in Canada’s aquatic environments.
Assessing the environmental impact is another key area of research for the Bilton team. Canada has a zero-discharge policy, meaning no oil can be present in water when discharging it back into our water systems. These regulations vary by country. Norway, for example, requires the amount of oil in the discharge to be less than 15 parts per million. Bilton and her team are running a parallel project funded through NRCan’s Multi-partner Research Initiative to understand the environmental impact and considerations of implementing this in-situ treatment process.
Bilton’s team is one of the five finalists moving on to Stage 3 of the competition, with the winner set to be announced in winter of 2025. At this stage, the team has one year to accelerate, scale and test their prototype in preparation for commercialization.
“We are in the testing phase now and are planning large-scale simulations at our Ohmsett partner facility in New Jersey,” says Bilton.
The team is partnering with Western and Eastern Coast Marine Response Corporations, VPC Group and Urethane Sciences to ensure their system is scalable and can be manufactured. The current prototype is significantly smaller – around one metre in size – than what the final system will be. Ensuring the engineered polymer foam and other materials can be manufactured and meet strict requirements are top of mind at this stage of the challenge.
“Our goal is that this system can be deployed quickly and effectively to improve oil spill response across Canada, and potentially in other parts of the world,” says Bilton.
The research team that wins the final stage will receive an additional $2 million in funding to commercialize their technology.